When you think about the foundry industry, it might sound like an old-school concept, but trust me, it's evolving faster than you can say "molten metal." This sector has been around for centuries, shaping the backbone of modern manufacturing, but today, it's undergoing a transformation that's nothing short of revolutionary. From ancient techniques to cutting-edge technology, the foundry industry is stepping into the future with bold strides, and you won't believe how far it's come.
Now, let's rewind for a moment. The foundry industry evolution hasn't been just about melting metal; it's been about pushing boundaries, solving problems, and creating solutions that impact everything from cars to spacecraft. It's a story of resilience, creativity, and relentless innovation. And if you're wondering why this matters, well, buckle up because the changes happening right now are set to redefine how we make almost everything around us.
So, whether you're a tech enthusiast, a manufacturing expert, or just someone curious about the magic behind the products we use daily, this article is for you. We're diving deep into the world of foundries, exploring how they've grown, the challenges they face, and the exciting opportunities ahead. Let's get started!
Read also:Natalie Reynolds Leaks The Untold Story Behind The Viral Sensation
Here's a quick rundown of what we'll cover:
- The Rich History of Foundries
- Modern Technologies in Foundries
- Challenges Facing the Foundry Industry
- Sustainability in Foundry Operations
- The Role of Automation in Evolution
- 3D Printing Revolutionizing Casting
- Global Trends in the Foundry Industry
- The Future of Foundries
- Economic and Social Impact
- Wrapping It All Up
The Rich History of Foundries
Let's kick things off with a little history lesson. The foundry industry has roots that go way back—like, ancient civilization back. Think about it: humans have been melting metals since before the common era. The earliest known castings date back to 3200 BC in Mesopotamia, where people crafted tools, weapons, and ornaments using bronze. Fast forward to the Middle Ages, and foundries were popping up all over Europe, fueling the industrial revolution with iron and steel.
But here's the kicker: what started as simple, manual processes has evolved into a complex, high-tech industry. Foundries back then relied heavily on human labor, but today, they're incorporating robotics, AI, and advanced materials to create components that are lighter, stronger, and more efficient. It's like comparing a horse-drawn carriage to a Tesla—it's still transportation, but the tech is worlds apart.
And let's not forget the cultural significance of foundries throughout history. They've been central to economic growth, military advancements, and even artistic expression. From the cannons of war to the statues of art, foundries have played a pivotal role in shaping human civilization. So, yeah, they're kind of a big deal.
Key Milestones in Foundry Evolution
- 3200 BC: The first recorded metal casting in Mesopotamia.
- 500 AD: Iron smelting becomes widespread in Europe.
- 1700s: The industrial revolution brings about mass production in foundries.
- 1900s: Introduction of electric furnaces and alloys.
- 2000s: Advanced materials and digital technologies take center stage.
Modern Technologies in Foundries
Now that we've got the history out of the way, let's fast-forward to today. The foundry industry evolution isn't just about preserving tradition; it's about embracing the future. Modern foundries are equipped with state-of-the-art technologies that would blow the minds of their ancestors. Take, for example, the use of computer-aided design (CAD) and computer-aided manufacturing (CAM). These tools allow engineers to design intricate molds and patterns with precision, reducing errors and saving time.
Then there's the rise of smart factories, where machines are connected through the Internet of Things (IoT). This means real-time monitoring, predictive maintenance, and optimized workflows. Imagine a foundry where every machine talks to each other, ensuring efficiency and minimizing downtime. Sounds futuristic, right? Well, it's happening right now.
Read also:Ambergianna Onlyfans The Rising Star In Digital Content Creation
And let's talk about materials. Gone are the days of just iron and steel. Today's foundries are experimenting with advanced alloys, composites, and even nanomaterials. These innovations are driving the development of lighter, stronger, and more durable components, which are essential for industries like aerospace and automotive.
Top Technologies Shaping the Foundry Industry
- IoT: Connecting machines for smarter operations.
- AI: Enhancing decision-making and process optimization.
- CAD/CAM: Revolutionizing design and production.
- Advanced Materials: Creating components with superior properties.
Challenges Facing the Foundry Industry
Of course, no journey is without its bumps in the road. The foundry industry evolution isn't all sunshine and rainbows. There are some serious challenges that foundries are grappling with, and they're not taking these issues lightly. One of the biggest hurdles is environmental regulations. With increasing pressure to reduce carbon emissions and waste, foundries are having to rethink their processes and adopt greener technologies.
Another challenge is the skills gap. As the industry becomes more tech-driven, there's a growing need for workers with expertise in areas like robotics, data analytics, and programming. But here's the catch: traditional foundry workers often lack these skills, and training programs are still catching up. It's like trying to teach a horse to drive a car—it's gonna take some time.
Global competition is also a big deal. Foundries in developing countries can often produce components at a fraction of the cost, thanks to lower labor and material expenses. This puts pressure on established foundries to innovate and find ways to stay competitive. It's a tough game, but one that's driving some pretty impressive advancements.
Overcoming Challenges in the Foundry Industry
- Environmental Regulations: Investing in sustainable practices.
- Skills Gap: Focusing on education and upskilling workers.
- Global Competition: Embracing innovation to stay ahead.
Sustainability in Foundry Operations
Speaking of sustainability, it's a hot topic in the foundry industry right now. Companies are realizing that going green isn't just good for the planet; it's also good for business. By adopting eco-friendly practices, foundries can reduce costs, improve efficiency, and meet consumer demand for sustainable products.
One way they're doing this is by recycling metal. Did you know that metal is one of the most recyclable materials on the planet? Foundries are taking advantage of this by incorporating recycled materials into their production processes. This not only cuts down on waste but also reduces the need for raw materials, which can be expensive and environmentally damaging to extract.
Energy efficiency is another big focus. Foundries are investing in energy-efficient furnaces, lighting, and machinery, as well as exploring alternative energy sources like solar and wind power. It's all about reducing the carbon footprint while maintaining productivity. And let's be honest, who doesn't love a win-win situation?
Key Strategies for Sustainable Foundries
- Recycling Metal: Reducing waste and conserving resources.
- Energy Efficiency: Cutting costs and emissions.
- Alternative Energy: Exploring renewable sources.
The Role of Automation in Evolution
Automation is another game-changer in the foundry industry evolution. By automating repetitive and dangerous tasks, foundries can improve safety, increase productivity, and reduce costs. Robots are now being used for everything from pouring molten metal to inspecting finished products. It's like having a team of superhuman workers that never get tired or injured.
But automation isn't just about replacing humans; it's about enhancing human capabilities. Workers can focus on more complex and creative tasks, while machines handle the grunt work. This not only boosts morale but also creates opportunities for career advancement. It's a partnership that's proving to be mutually beneficial.
And let's not forget about data. Automation generates tons of data, which can be analyzed to optimize processes, predict maintenance needs, and improve quality control. It's like having a crystal ball that tells you exactly what's going on in your foundry at any given moment. Who wouldn't want that?
Benefits of Automation in Foundries
- Improved Safety: Reducing risks for workers.
- Increased Productivity: Getting more done in less time.
- Data-Driven Insights: Making smarter decisions.
3D Printing Revolutionizing Casting
Now, let's talk about 3D printing, because it's seriously shaking things up in the foundry industry. This technology allows for the creation of complex molds and patterns that would be impossible to produce using traditional methods. It's like giving foundries superpowers to create anything they can imagine.
But here's the thing: 3D printing isn't just for show. It's also cost-effective, especially for small-scale production runs or custom components. Instead of investing in expensive tooling, foundries can print molds on demand, saving both time and money. It's a game-changer for industries that require rapid prototyping and customization.
And the best part? 3D printing is compatible with a wide range of materials, from plastics to metals. This opens up endless possibilities for innovation and creativity. Whether it's creating lightweight parts for airplanes or intricate designs for jewelry, 3D printing is proving to be a valuable asset in the foundry industry evolution.
Applications of 3D Printing in Foundries
- Rapid Prototyping: Speeding up the design process.
- Custom Components: Meeting unique customer needs.
- Complex Designs: Pushing the boundaries of creativity.
Global Trends in the Foundry Industry
As the world becomes more connected, so does the foundry industry. Global trends are shaping the way foundries operate, from supply chain management to market demand. One of the biggest trends is the shift towards customization. Consumers are no longer satisfied with one-size-fits-all solutions; they want products that are tailored to their specific needs. This is driving foundries to adopt flexible manufacturing processes that can adapt quickly to changing demands.
Another trend is the rise of emerging markets. Countries like India, China, and Brazil are becoming major players in the foundry industry, thanks to their growing economies and increasing industrialization. This presents both opportunities and challenges for established foundries, as they navigate the complexities of global competition.
Finally, there's the issue of geopolitical factors. Trade policies, tariffs, and geopolitical tensions can have a significant impact on the foundry industry, affecting everything from raw material prices to export markets. It's a delicate balancing act that requires strategic planning and adaptability.
Key Global Trends in the Foundry Industry
- Customization: Meeting unique customer needs.
- Emerging Markets: Expanding opportunities in developing countries.
- Geopolitical Factors: Navigating trade policies and tensions.
The Future of Foundries
So, where is the foundry industry headed? If you ask me, the future looks bright. With advancements in technology, materials, and sustainability, foundries are poised to play a crucial role in shaping the industries of tomorrow. From electric vehicles to space exploration, the demand for high-quality, innovative components is only going to grow.
But here's the thing: success won't come easy. Foundries will need to continue investing in R&D, training their workforce, and embracing change. It's not about resting on their laurels; it's about staying ahead of the curve and being willing to adapt. The foundry industry evolution is far from over, and the best is yet to come.
And let's not forget the
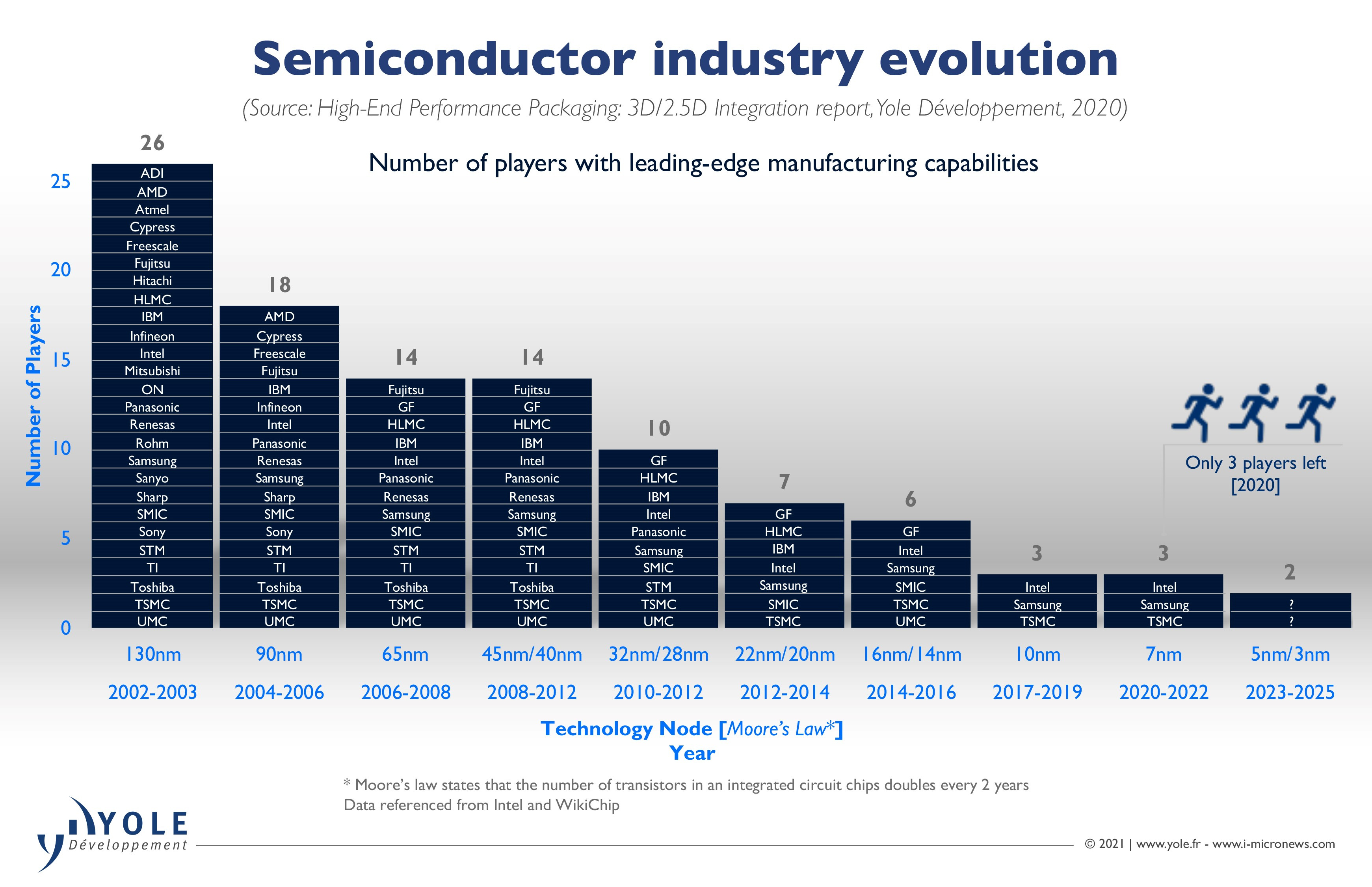
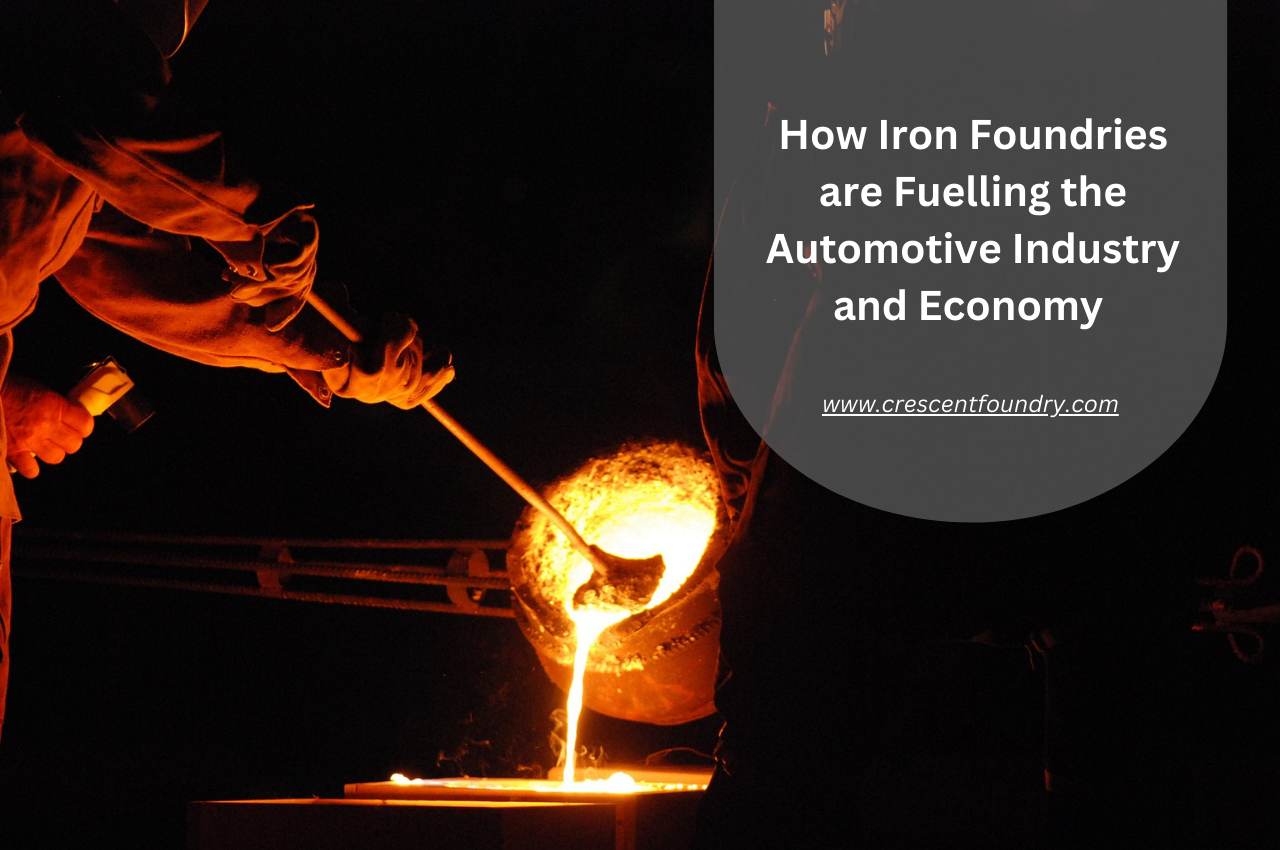