Imagine this—you’re cruising along with your routine maintenance schedule, thinking everything’s on point. But then, BAM! Unexpected challenges hit you out of nowhere. It’s like life’s way of reminding you that even the most meticulous plans can go sideways. And trust me, in the world of maintenance, those surprises can be costly and time-consuming. That’s why understanding these unexpected hurdles is crucial to keep your operations running smoothly.
In this article, we’ll dive deep into the realm of routine maintenance, exploring not just the basics but also the curveballs that might throw you off course. Whether you’re managing equipment, vehicles, or facilities, these insights will help you stay ahead of the game. And hey, who doesn’t want to be prepared for the unexpected?
So buckle up, because we’re about to break down what routine maintenance really entails, the common pitfalls, and—most importantly—how to tackle those unexpected challenges head-on. This isn’t just another guide; it’s your ultimate toolkit for staying proactive and avoiding costly downtime.
Read also:Why Uchi No Otouto Is More Than Just A Manga Series
What Exactly is Routine Maintenance?
Let’s start with the basics. Routine maintenance refers to the regular upkeep and servicing of equipment, machinery, or systems to ensure they continue operating efficiently and safely. It’s like giving your car a regular tune-up to keep it running smoothly. The goal? To catch potential issues before they escalate into major problems.
Now, here’s the kicker—routine maintenance isn’t just about following a checklist. It’s about understanding the unique needs of your assets and tailoring your approach accordingly. Some systems might require daily checks, while others might only need quarterly inspections. It all depends on the nature of the equipment and its usage.
Why Routine Maintenance Matters
Think of routine maintenance as your first line of defense against equipment failure. Without it, you’re essentially rolling the dice every day, hoping nothing breaks down. And when it does—oh boy—those repair costs can hit hard. Not to mention the downtime that could disrupt your entire operation.
- Reduces the likelihood of unexpected breakdowns.
- Extends the lifespan of your equipment.
- Improves overall efficiency and productivity.
- Saves you money in the long run by avoiding costly repairs.
But here’s the thing: while routine maintenance is a powerful tool, it’s not foolproof. That’s where those unexpected challenges come into play.
Understanding the Unexpected Challenges
Now that we’ve established the importance of routine maintenance, let’s talk about the elephants in the room—the unexpected challenges. These are the curveballs that can throw even the most seasoned maintenance pros off their game. They might come in the form of sudden equipment failures, supply chain disruptions, or even human error.
And let’s be real, no one plans for these. But understanding their root causes can help you prepare for them. So, what are these challenges, and how can you tackle them?
Read also:Brandy Renee Leak Unveiling The Truth Behind The Headlines
Challenge #1: Equipment Failures
Even with the best maintenance schedule, equipment can still fail unexpectedly. It’s frustrating, but it happens. The key is to identify the signs early and take corrective action before it’s too late.
Some common causes of unexpected equipment failures include:
- Wear and tear beyond normal expectations.
- Improper usage or overloading.
- Defective parts that weren’t caught during inspections.
Regularly reviewing your maintenance logs can help you spot patterns and address potential issues before they become major problems.
Challenge #2: Supply Chain Disruptions
We’ve all heard the stories—supply chains getting disrupted due to unforeseen events like natural disasters, pandemics, or geopolitical tensions. When you can’t get the parts you need, your maintenance schedule can go haywire.
Here’s how you can mitigate the impact:
- Establish relationships with multiple suppliers.
- Keep a stockpile of critical spare parts on hand.
- Stay informed about global events that could affect your supply chain.
Being proactive in this area can save you a lot of headaches down the road.
Strategies for Overcoming Unexpected Challenges
Alright, so we’ve identified some of the major challenges. But how do you actually overcome them? Let’s break it down into actionable strategies that you can start implementing today.
Strategy #1: Invest in Predictive Maintenance
Predictive maintenance uses data and analytics to predict when equipment is likely to fail. It’s like having a crystal ball for your maintenance needs. By monitoring key metrics like vibration, temperature, and pressure, you can catch potential issues before they become critical.
Some benefits of predictive maintenance include:
- Reduced downtime.
- Lower maintenance costs.
- Improved equipment reliability.
While it requires an initial investment in technology and training, the long-term savings can be substantial.
Strategy #2: Develop a Comprehensive Maintenance Plan
Having a solid maintenance plan in place is crucial for tackling unexpected challenges. This plan should include:
- Clear maintenance schedules for all equipment.
- Defined roles and responsibilities for your maintenance team.
- Protocols for addressing emergencies.
Regularly reviewing and updating this plan ensures that you’re always prepared for whatever comes your way.
Building a Resilient Maintenance Team
Your maintenance team is the backbone of your operation. Without them, even the best-laid plans can fall apart. So how do you build a team that can handle anything thrown their way?
Tips for Building a Strong Team
- Invest in ongoing training and development.
- Foster a culture of collaboration and communication.
- Empower team members to take ownership of their roles.
Remember, a well-trained and motivated team is your best defense against unexpected challenges. Encourage them to share ideas and feedback, and make sure they feel valued and supported.
Technology: Your Secret Weapon
In today’s digital age, technology can be your biggest ally in managing routine maintenance. From mobile apps to IoT devices, there are countless tools available to help you stay on top of your game.
Key Technologies to Consider
- Computerized Maintenance Management Systems (CMMS).
- Sensor-based monitoring systems.
- Cloud-based data storage and analytics.
These technologies not only streamline your processes but also provide valuable insights that can help you make informed decisions.
Case Studies: Real-World Examples
Let’s take a look at some real-world examples of organizations that have successfully navigated unexpected maintenance challenges.
Example #1: A Manufacturing Plant
A large manufacturing plant faced unexpected downtime due to a critical machine failure. By implementing predictive maintenance and investing in a robust CMMS, they were able to reduce downtime by 40% and save over $500,000 in repair costs annually.
Example #2: A Fleet Management Company
A fleet management company struggled with supply chain disruptions during a global pandemic. By diversifying their supplier base and maintaining a stockpile of essential parts, they were able to keep their operations running smoothly despite the challenges.
Cost Implications of Ignoring Maintenance Challenges
Ignoring the unexpected challenges of routine maintenance can have serious financial consequences. Downtime, repair costs, and lost productivity can quickly add up, eating into your bottom line.
Here are some key statistics to consider:
- Unplanned downtime costs industrial manufacturers an estimated $50 billion annually.
- Equipment failure is responsible for 42% of unplanned downtime.
- Predictive maintenance can reduce maintenance costs by up to 40%.
These numbers speak for themselves. Investing in a proactive maintenance strategy is not just a good idea—it’s a necessity.
Final Thoughts: Stay Proactive, Stay Prepared
So there you have it—a comprehensive guide to routine maintenance and the unexpected challenges that come with it. By understanding these challenges and implementing the right strategies, you can keep your operations running smoothly and avoid costly surprises.
Remember, routine maintenance isn’t just about following a checklist. It’s about staying proactive, leveraging technology, and building a resilient team. And when the unexpected does happen—and it will—you’ll be ready to handle it with confidence.
Now it’s your turn. Share your thoughts in the comments below. Have you faced any unexpected maintenance challenges? How did you tackle them? And don’t forget to check out our other articles for more insights and tips.
Table of Contents
- What Exactly is Routine Maintenance?
- Why Routine Maintenance Matters
- Understanding the Unexpected Challenges
- Challenge #1: Equipment Failures
- Challenge #2: Supply Chain Disruptions
- Strategies for Overcoming Unexpected Challenges
- Strategy #1: Invest in Predictive Maintenance
- Strategy #2: Develop a Comprehensive Maintenance Plan
- Building a Resilient Maintenance Team
- Technology: Your Secret Weapon
- Case Studies: Real-World Examples
- Cost Implications of Ignoring Maintenance Challenges
- Final Thoughts: Stay Proactive, Stay Prepared
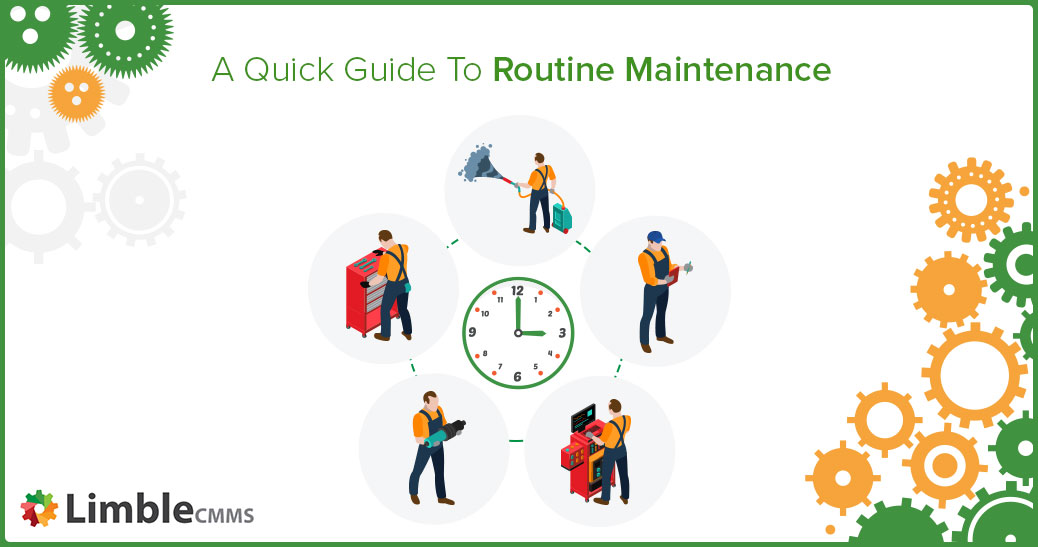
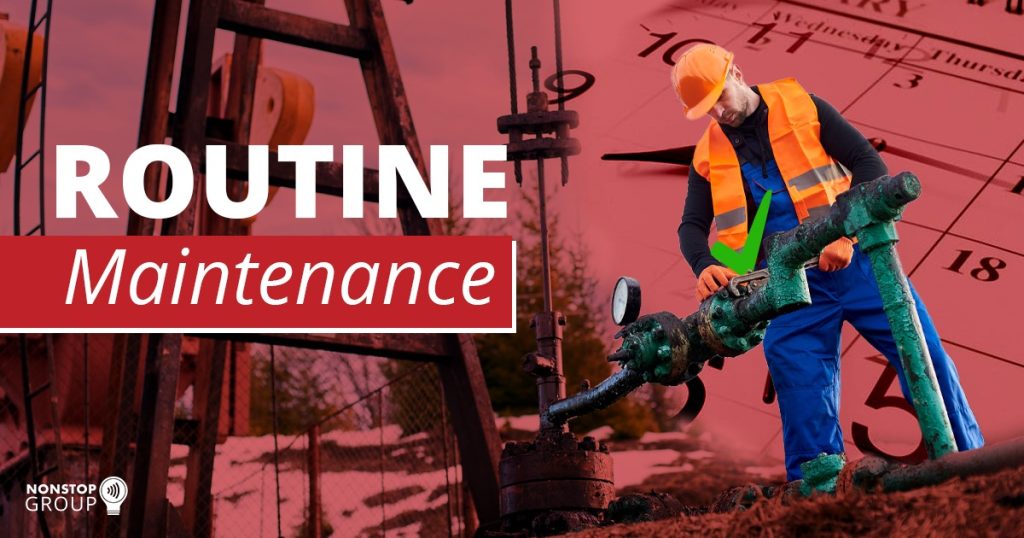
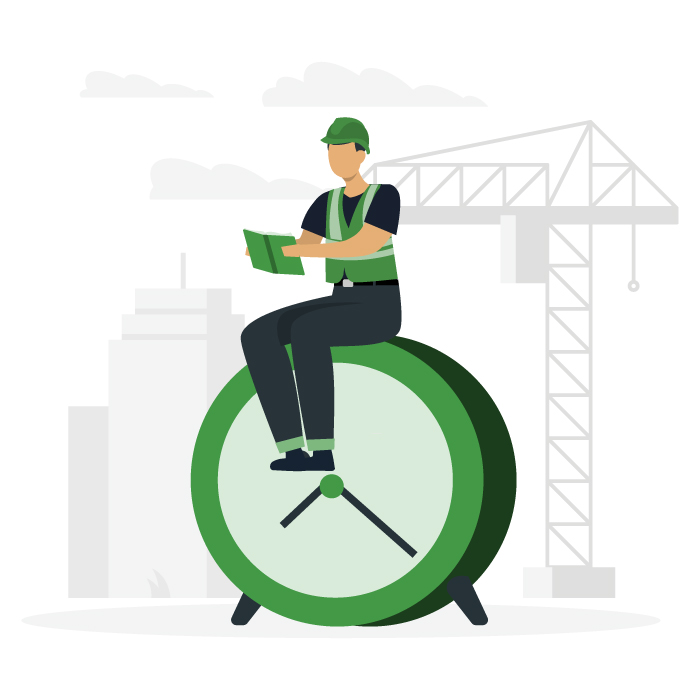